Sustainable Supply Chain Practices to Decarbonise Steel Industry by AM/NS India CASE STUDY
This is a Case Study on AMNS India, in which I have covered 3 topics.
- Sustainable Supply Chain practices implemented by AM/NS India to decarbonise the steel industry.
- Additional Sustainable Supply Chain Practices for Large Scale Heavy Manufacturing Industries to reduce Carbon Footprint/Net Zero CO2 emissions.
- Benefits of Building a Sustainable Supply Chain Nowadays.
Sustainable Supply Chain practices implemented by AM/NS India to decarbonise the steel industry
AMNS India is a joint venture (60:40) between ArcellorMittal and Nippon Steel Corporation. AMNS India acquired Essar Steel India Limited (ESIL) in 2019. Since then AMNS have acquired several manufacturing, power and infrastructure facilities to strengthen their entire supply chain.
Slurry Pipelines for transporting Iron Ore
Problems faced in transporting the Iron Ore via road.
- Transportation of Iron Ore through Roads causes heavy environmental degradation which is difficult to measure.
- Diesel powered trucks have high maintenance cost and their co2 emissions are way to high.
- During rains, it gets more difficult to transport the Iron Ore through trucks, as they are not covered from the top, damaging the material in transit.
But once the construction of the Slurry pipeline is completed from Sagasahi to Dabuna, trucks would not be needed anymore. These pipelines will easily transport the iron ore from point A to point B. Weather can no longer have any effect on slurry pipelines. The cost of transportation gets reduced significantly and so does the carbon footprint.
This project by AMNS India has safely secured the interest of all community concerns, while safeguarding the environment.
Just one question though.
What will happen to the trucks or the truck drivers who will not be needed anymore, once the construction of the slurry pipelines gets completed?
I hope AMNS India has planned something good for them too in the future.
Using Riverine Jetty instead of Trucks
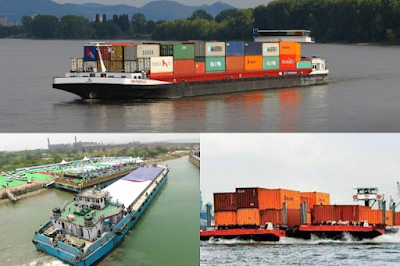
This jetty will then be used to transport the imported raw materials from the Paradip port to the pellet plant and outbound material from the pellet plant to the Paradip port. This will eliminate the need for trucks and reduce the carbon emissions.
The company also says that this project will create more than 300 jobs.
Riverine Jetties are good for transporting bulk cargo and are really the cheapest mode of transport.
Using Renewable Energy to Power Low Carbon Steelmaking

ArcellorMittal is the parent company of AM/NS India (ArcellorMittal Nippon Steel India). ArcellorMittal have partnered with Greenko Group, who will design, build and handle a renewable energy power project.
The project will include solar power, wind power and Greenko’s supported Hydro Pumped storage. It will have a nominal capacity of 975 MW.
AMNS India has entered into an agreement with ArcellorMittal for 25 years, in which AMNS will receive 250 MW renewable energy annually. And this 250 MW will cover 20% of the actual electricity demand at their Low Carbon Steel Making plant in Hazira, Gujarat.
This Renewable energy will reduce the carbon emissions at AMNSIndia by 1.5 Million Tonnes per annum.
Other Benefits include:
- Reduced electricity cost for the company.
- Creates more jobs than fossil fuel energy industry.
- A source of energy that can never run out, Wind and Sun.
- Promotes sustainable means of manufacturing steel operations.
- Reducing the use of Coal with Industrial LNG.
AM/NS India partnered with Total Energies (Paris) to supply 5 hundred thousand tons of Industrial LNG annually, till 2026.
LNG will now be used to run their steel plants and power plants in Gujarat.
Industrial LNG will not completely replace the use of coal but will definitely reduce the dependency on coal. Thereby, reducing carbon emissions significantly, if not completely.
Coal is basically a non-renewable form of energy. There are large reserves of coal globally, but it still degrades the environment.
Using Steel Slag to prevent Coastal Erosion
80 percent of the raw material used in these tetrapods or blocks is sand and granite stone chips.
AM/NS India took this opportunity in an effort to push their companies sustainable manufacturing practices. And they have started processing their steel slag into fine and coarse forms. These processed steel slags are now being applied in manufacturing the high density coastal tetrapods as a complete replacement for sand and stone chips.
Using Steel Slag to build Roads
AMNS India generates a total of 2.5 MTPA of steel slag. In Gujarat, the company has used 1 lakh tonnes of processed steel slag to construct a 1.2 km road with six lanes.
Further, today steel slags can be used as an alternative to filler in filling road pavements, in construction material to replace concrete and its powdered form can be used as a fertiliser in agriculture industry.
Additional Sustainable Supply Chain Practices for Large Scale Heavy Manufacturing Industries to reduce Carbon Footprint/Net Zero CO2 emissions
- Redesigning the entire Logistics from the start of the supply chain to the end. Replace all the diesel powered trucks with electric trucks. Have an electric charging infrastructure in place for company vehicles.
- Switch completely to Renewable Source of Energy, that is Wind Energy and Solar Energy. Deploy the use of renewable sources of energy in the entire supply chain, from manufacturing plant to warehouse to distribution centre to company owned retail outlets.
- Monitor, track and trace the waste generated at the production site, manufacturing plant, warehouses, distribution centres and the scrap generated after the entire life cycle of the steel products. And reuse or recycle them.
- Build a water management system and limit the usage of water at all the facilities. Also, install meters to track the usage of water in the company.
- Use rail transportation instead of road wherever possible, and use water transport instead of rail wherever possible.
Benefits of Building a Sustainable Supply Chain Nowadays
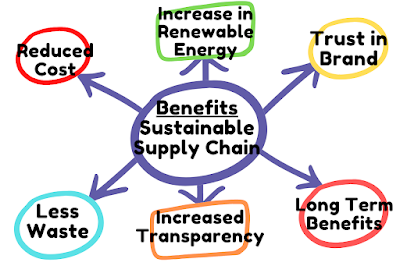
- Reduction in costs across the entire supply.
- Reducing the dependency on fossil fuels, helps in reducing the carbon emissions.
- Helps you position your brand in the eyes of your customer. Today, customers are more concerned about how everything is being produced whatever they are consuming.
- The capital expenditure may increase in the beginning, but these investments are going to create long term benefits.
- Creates transparency across your entire supply chain, thereby enhancing your brand reputation.
- Less damaging to the environment.
- More energy efficient operations and generates less waste.